AR Products are patented, tested and proven for
long-term performance.
Anti-Galloping Device Technology
AR Products specializes in galloping control solutions. Variations in wind, ice, dynamic structural properties and conductor stiffness under changing environmental conditions makes galloping difficult to predict. The AR method of application and proprietary twisting technology of AR dampers has been shown to reduce predicted peak-to-peak galloping amplitude by more than 50%.
Understanding Twisting Technology
Twisting the conductor as a method to control galloping is a complex challenge. AR Products specializes in designing a solution suitable for the unique characteristics and features of the line. Experience has shown that dampers that twist the conductor will act to arrest galloping, rather than merely decrease galloping amplitude.
How Twisting Works to Control Galloping
As the wind angle of attack creates galloping conditions, the gravitational force on the damper will cause the conductor to start twisting, thus dumping off the aerodynamic lift. AR Products solutions control galloping by twisting the conductor, a methodology based on two key principles: acceleration and inertia.
Using Twisting as a Method to Control Galloping
Twisting technology differentiates AR Products anti-galloping solutions from all others. The initial twist of the line at product installation induces the conductor to rotate through large angles when ice and wind conditions occur, so that galloping never gets going.
This initial twist and gravitational forces on the anti-galloping dampers will cause the conductor to start twisting more during wind and ice conditions, effectively dumping off the aerodynamic lift that induces galloping.
AR Products technology is grounded in fundamental, scientific and engineering principles.
Comparing effective galloping control between AR Products and Interphase Spacers
PacifiCorp Gets a Grip on Galloping Conductors - "On-line devices tame wind- and -ice induced conductor movement."
What does Galloping look like?
A field test to show how twisting controls galloping amplitude
Problem
Solution
Product Testing
Holding Strength.* Two models of AR Clamps have been tested for holding strength. Alligator grip clamps slipped at a tensile load of 1000 lbs. Nutcracker grip clamp slipped at a tensile load of 1200 lbs.
AR Clamp Holding Test
AR Clamp Corona Testing 2010
Corona and RIV Testing* AR Clamps and Spacer Dampers have been tested for RIV measurements and corona photographs. RIV and Corona tests indicate AR Clamps are free of corona ad RIV well above 345kV.
Corona/RFI Testing of the AR®Clamp AR®Spacer Damper
Corona/RFI Testing of the AR Clamp with Neoprene
Insulator Rod Testing.* Insulator rods used in the AR Spacer Twister have been tested for compressive strength to establish column-buckling behavior. The tensile test of the 5/8” rod revealed an ultimate load of 35,000 lbs. The rods behave as an elastic column under compression load.
Spacer Twister Insulator Rod Tests
Galloping and Vibration Performance Testing.* AR Twister have been tested to qualify for performance in controlling Aeolian vibration and galloping on energized high voltage transmission lines. Testing also included corona and RIV.
AR Damper Vibration and High Voltage Tests
Dynamic & Mechanical Testing.* AR Clamps, Twister and Spacer Damper have been test for mechanical characteristics and tensile strength.
Dynamic & Mechanical Testing of MOD 2
Mechanical Testing of AR Clamp
All tests were completed in an independent laboratory.
Field Studies
Research Consulting Associates has conducted scores of research and development projects for private industry entities, as well as Federal Government agencies, including the NSF, DOE and NASA. Research includes examining methods for effectively controlling high-frequency vibration and low frequency galloping of power lines. Field studies include measuring product performance and the analysis of data on galloping.
Studying the Probability of Galloping. In 1998, Research Consulting Associates pioneered one of the most comprehensive studies on galloping based on field data collected over 3 years. Funded by the Department of Energy, the study analyzed data collected by Ontario Hydro on the field performance of two anti-galloping dampers. Several hundred units of each damper were installed on the utility’s single circuit line for observation. One conclusion of this study was that the probability of galloping is a linear function. The other lesson learned from both this study, and experience, is that galloping is a phenomenon that cannot be controlled in a single span approach. Observed galloping in one span may have started in an adjacent one, and it may then relay the motion in both directions ahead and back. Treating one span where galloping has been observed does guarantee that the line will not gallop again nor will it protect adjacent spans from galloping. See A Study of Galloping Conductors on 230kV Transmission Line
Twister. PacifiCorp analyzed the Worland to Thermopolis line in Wyoming to determine the probability of conductor clashing. Field testing was initiated to compare effective galloping control by the AR Spacer Twister (polymer interphase with articulating clamps) and the AR Twister MOD3 (20lbs aluminum weight). These tests revealed that both devices eliminated galloping flashover. See PacifiCorp gets a Grip on Galloping Conductors, T&D World/April 2002.
Spacer Damper. A series of field tests were undertaken during December 1985 in Littleton, New Hampshire, for the New England Power Company to measure the Aeolian vibration of a new triple bundle DC transmission line. The objective was to evaluate the performance of the damping devices installed on the Phase I transmission line. These tests provided design data for specifying vibration control devices for the Phase II line. Conclusions of the study included:
• vibration of a single conductor is 4-5 times less than the vibration of the triple bundle having five spacer-dampers of a particular type, and
• the level of vibration of the bundle having only one spacer-damper at mid-span and one end-point damper per sub-conductor is the same as a single conductor. See Vibration of Bundled and Single Conductors: A Comparative Case Study
Patents
MEANS FOR DAMPING VIBRATIONS OF POWER TRANSMISSION LINES
United States Patent 3,440,328
Windamper
ANTI-GALLOPING DEVICE, TRANSMISSION LINE COMBINED THEREWITH, AND METHODS
United States Patent 4,777,327
Twisting as a Method for Controlling Galloping of Transmission Lines
TRANSMISSION LINE SPACER DAMPER DEVICE
United States Patent 5,362,920
AR Spacer Damper for Twin, Triple and Quad Bundled Transmission Lines
METHOD OF SPACING TRANSMISSION LINE SUBCONDUCTORS
United States Patent 5,488,920
Method for Controlling Galloping of Bundled Transmission Lines
TRANSMISSION LINE SPACER DAMPER DEVICE MOD-II
United States Patent 5,721,393
AR Spacer Damper MOD2
TRANSMISSION LINE SPACER TWISTER DEVICE
United States Patent 6,008,453
AR Spacer Twister
SPACER DEVICE
United States Patent 8,981,227
United States Patent 10,014,677
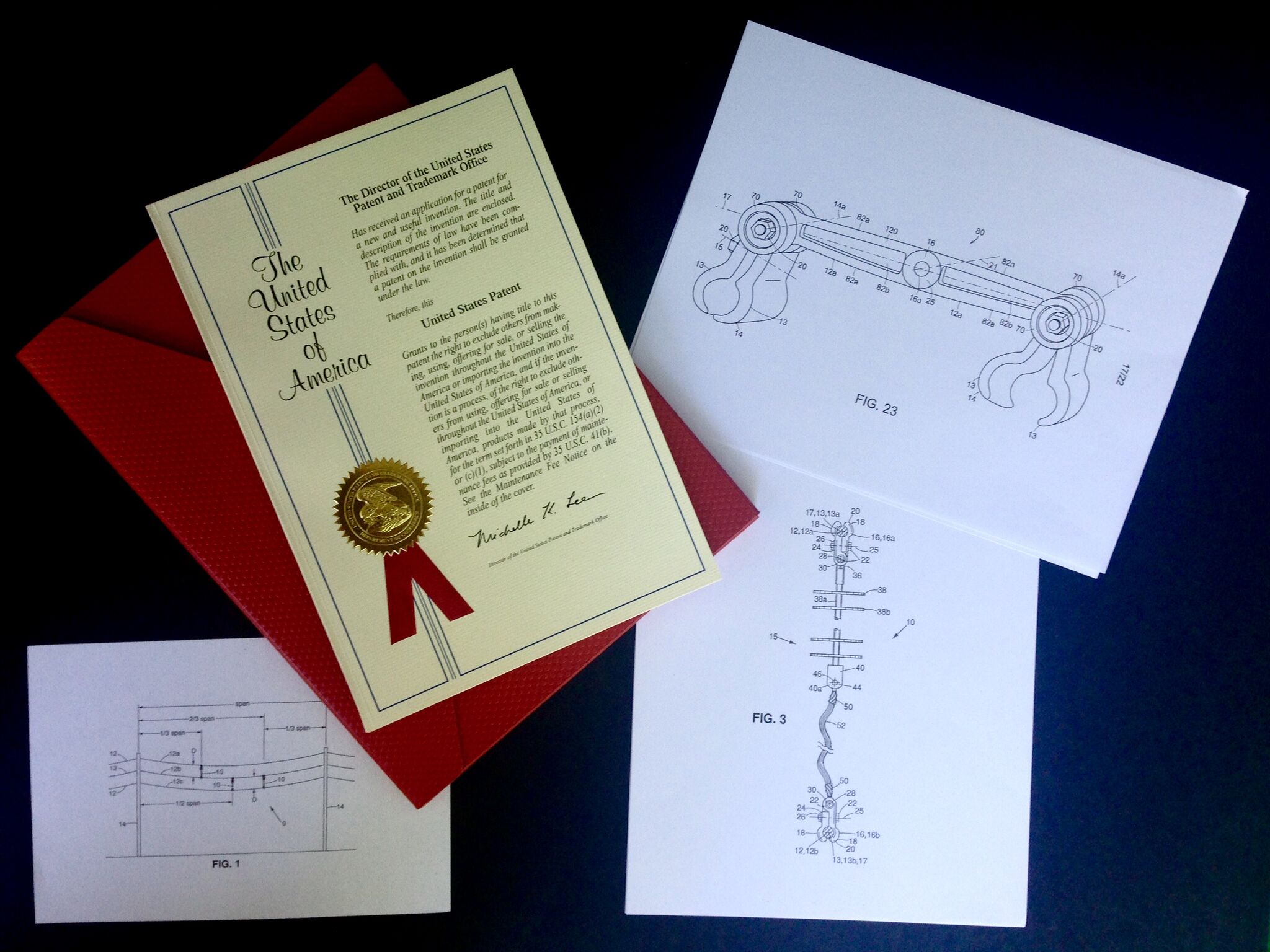